Fronius på EuroBLECH
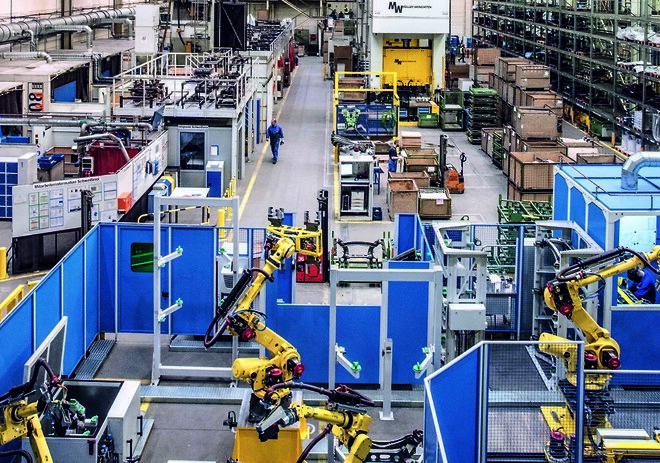
På grunn av disse fordelene var den anerkjente stålprodusenten og bilunderleverandøren voestalpine det første selskapet som valgte å bruke den avanserte CMT-teknologien i serieproduksjon – og det med stor suksess.
- Den andre generasjonen til CMT-prosessen representerer et skikkelig kvantesprang sammenlignet med den forrige versjonen, selv om sistnevnte allerede ga sveisekvalitet og prosessikkerhet på høyeste nivå, forklarer Michael Nowasz entusiastisk etter tre måneder med serieproduksjon. For lederen innen sammenføyning hos voestalpine Automotive Components Schmölln GmbH er det én ting som er sikkert:
- Vi har økt kvaliteten ytterligere takket være de mange fornyelsene og videreutviklingen av TPS/i i kombinasjon med en skreddersydd CMT-prosess og i tillegg utvidet vår fleksibilitet innen sammenføyning i betydelig grad.
Som den forrige generasjonen utmerker den nye CMT-prosessen (Cold Metal Transfer) seg med en spesielt lav varmetilførsel og en høy fugefylling. Dette oppnås med en spesielt dynamisk styring av lysbuen. - Tilnærmingen Fronius har valgt, skiller seg ut fra andre ved første øyekast, fordi dråpeløsningen eller dråpeovergangen ikke bare styres av strømkildens elektronikk, men også støttes mekanisk, sier fagområdelederen. Til dette formål trekkes trådelektroden alltid litt tilbake ved hjelp av en Push-Pull-sveisepistol når strømmen har nådd maksimum og slås av. Dette gir en spesielt stabil lysbue som arbeider uten sprut og tillater høyere sveisehastigheter.
Kvalitet i fokus: raskere sveising med CMT- Ved å bytte fra standard-MAG-prosess til CMT har vi allerede oppnådd en tilfredsstillende ytelsesøkning, sier Michael Nowasz når han ser tilbake på perioden etter at de innførte den første generasjonen til CMT-prosessen ved Schmölln-anlegget i 2011.
- Etter denne omstillingen må vi nesten ikke fjerne sprut lenger, og dermed kan medarbeidere mine ha fullt fokus på det våre oppdragsgivere fra bilindustrien er avhengige av: sveisesømmens kvalitet.
En annen fordel med CMT-løsningen fra Fronius er den høye tilgjengeligheten til CMT-anlegget, understreker fagområdelederen:
- Skulle lysbuen av en eller annen grunn slukne, tennes prosessen av seg selv igjen. Tenningsfeil og at trådelektroden brenner seg fast til kontaktrøret eller lignende irriterende hendelser tilhører fortiden hos oss.
Sist men ikke minst setter sammenføyningsspesialisten pris på de mange mulighetene Fronius tilbyr til å påvirke sveiseprosessen eller lysbuegeometrien. Dette inkluderer også muligheten til å kombinere CMT med en pulsprosess for å kunne styre varmetilførselen via lysbuen til grunnmaterialet enda bedre og sveise desto raskere.
CMT inkludert i heftet over produktkrav for nye anleggPå grunn av de gjennomgående positive erfaringene har fagområdelederen sørget for at CMT-prosessen for lysbuesveising av stålplater på opptil 3 mm ble inkludert som standardprosess i heftet over produktkrav for nye sveiseanlegg. På disse anleggene produserer voestalpine et bredt utvalg av bilkonstruksjonsdeler av galvaniserte og høyfaste plater samt aluminiumplater. Sist arbeidet seks av tolv robotsveiseceller ved Schmölln-anlegget med CMT-prosessen.
De ansvarlige hos voestalpine reagerte derfor svært positivt på CMT-teknologiens andre generasjon som ble presentert i begynnelsen av 2016, og på forslaget til Fronius om å teste bruken i serieproduksjon.
- Vi valgte en A-søyle av høyfast, galvanisert stål til de første sveiseforsøkene. Denne komplekse komponenten egner seg utmerket til å teste den nye prosessen svært grundig, ikke bare på grunn av det krevende materialet, men også på grunn av den begrensede tilgjengeligheten og de produksjonsrelaterte store spaltemålene, forklarer Michael Nowasz.
"Rett og slett genial"Sommeren 2016 ble de første sveiseforsøkene med den nye CMT-prosessen og TPS/i gjennomført på den tekniske fagskolen ved hovedkontoret til Fronius i Wels.
- Jeg besøkte laboratoriet sammen med vår utviklingsleder og opplevde den nye CMT-prosessen i aksjon, forteller fagområdelederen, og legger til:
- Det vi fikk se der, var rett og slett genialt. Vi skjønte umiddelbart at Fronius hadde gjort stor suksess igjen.
TPS/i danner grunnlaget for dette teknologiske fremskrittet. Det er ikke en enkel videreutvikling av den forrige modellen TPS, men en strømkilde som er designet på nytt fra grunnen av. Fronius utviklet alle komponentene på nytt, fra styringen via kommunikasjonsbussen og trådmateren til brukergrensesnittet, kjølesystemet og slangepakken. På denne måten kunne selskapet bruke den nyeste teknologien og dermed optimalisere hele systemet for maksimal presisjon og ytelse.
Ny algoritme – ny robotsveisepistolFor at CMT-prosessen skal ha størst mulig nytte av TPS/i, ble algoritmen satt opp på nytt og utvidet for andre generasjon. Push-Pull-sveisepistolen, som fikk helt ny design til TPS/i-serien, ble heller ikke oversett og ble som CMT-variant utstyrt med en digitalt styrt, girløs AC-servomotor for enda høyere frekvenser fra den oscillerende trådelektrodebevegelsen.
- En av fordelene med den nye robotsveisepistolen Robacta DriveMan legger man umiddelbart merke til. Den er mer kompakt enn den forrige modellen og gir dermed bedre tilgjengelighet – noe vi i økende grad trenger til mer komplekse komponenter, sier Michael Nowasz.
Ny CMT-prosess i serieproduksjonenResultatene av sveiseforsøkene på den virkelige komponenten var så overbevisende at deltakerne umiddelbart konverterte til den nye CMT-generasjonen for serieproduksjonen hos voestalpine. Allerede høsten 2016 var det klart. I løpet av en dag ble den første av seks robotceller endret av Fronius-medarbeidere. På denne robotcellen produseres holdere av blank, 2 til 3 mm tykk stålplate under CO2-beskyttelsesgass. Det legges omtrent en meter sveisesøm som er satt sammen av 48 enkeltsømmer med en maksimal lengde på 35 mm.
- Allerede neste formiddag lærte vi opp roboten og sveiset de første sømmene samme dag, minnes Michael Nowasz.
- Det viste seg at man kan finne mye raskere og lettere frem til de riktige sveiseparameterne med det nye systemet. På den tredje dagen var det bare nødvendig å etterjustere litt for å få de optimale arbeidsverdiene.
Fagområdelederen ble også imponert over funksjonaliteten til den nye magnetiske CrashBox:
- Vi lot roboten kjøre sveisepistolen mot en plate – beskyttelsesinnretningen utløste seg så raskt at det ikke oppsto skade på sveisepistolen, roboten, enheten eller arbeidsemnet.
Etter kollisjonen må den magnetiske låsen kobles på igjen, samtidig som referansepunktet beholdes, slik at man kan gjenoppta sveisingen med en gang. Det tungvinte byttet av CrashBox og referansekjøringen er dermed ikke lenger nødvendig.
Etter testene kunne voestalpine starte serieproduksjon med den nye CMT-konfigurasjonen allerede samme dag.
- Jeg ble veldig imponert over at omstillingen gikk så problemfritt og at det frem til i dag – tre måneder og 3000 deler senere – ikke har vært stillstand, og så langt har vi heller ikke vært nødt til å be om mer støtte fra Fronius, sier Michael Nowasz fornøyd.
Fronius stiller ut på tynnplatemessen EuroBLECH i Hannover 23. til 26. oktober i år. Du finner selskapet i hall 13 standF174
Kilde: Fronius
For mer informasjon se: www.fronius.no
Fakta:Forretningsområdet Perfect Welding
Fronius Perfect Welding er, ifølge selskapet, innovasjonsleder innen lysbue- og motstandspunktsveising og den globale lederen innen robotstyrt sveising. Som systemleverandør leverer Fronius Welding Automation også kundespesifikke, automatiserte og komplette sveiseløsninger, for eksempel for beholderkonstruksjon eller for cladding i offshore-sektoren. Strømkilder for manuelle applikasjoner, sveiseutstyr og et bredt spekter av tjenester kompletterer porteføljen. Med over 1000 salgspartnere over hele verden er Fronius Perfect Welding svært nær kunden.
Fronius International GmbH
Fronius International er et østerriksk selskap med hovedsete i Pettenbach og med øvrige anlegg i Wels, Thalheim, Steinhaus og Sattledt. Selskapet har 4550 ansatte på verdensbasis og arbeider innenfor områdene sveiseteknikk, solcelleteknologi og batteriladeteknikk. Fronius har 30 internasjonale selskaper og representanter i over 60 land. Dette gir en eksportandel på cirka 91 prosent. Innovative produkter og tjenester samt 1241 tildelte patenter gjør, ifølge selskapet, Fronius til innovasjonsleder på verdensmarkedet.