Suksess for automatisert metallisk 3D-printing
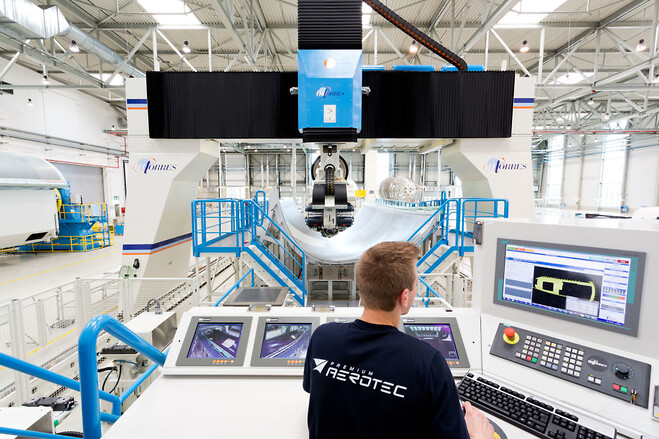
3D-printprosessen, på engelsk kjent som "Additive Manufacturing" (AM), er blitt mer og mer interessant som en komplementær eller alternativ prosess til konvensjonelle produksjonsteknikker. Teknologien er beskrevet som "additiv" på grunn av måten prosessen involverer påføring av lag etter lag av tynt materiale, som deretter herdes av en energikilde. Sammen med plast og keramikk er det også mulig å produsere metallkomponenter i en 3D-print.
50 prosent kostnadsreduksjonFormålet med pilotprosjektet var å utvikle en digitalisert neste generasjons produksjonslinje som kunne produsere aluminiumkomponenter til bil- og luftfartssektoren betydelig mer kostnadseffektivt enn det er mulig for øyeblikket. Det vellykkede resultatet av NextGenAM: Med hensyn til den overordnede produksjonsprosessen ved Premium AEROTEC, kan produksjonskostnadene reduseres med opptil 50 prosent sammenlignet med eksisterende 3D-printsystemer.
- Med hensyn til flyindustrien er Premium AEROTEC i dag allerede en internasjonal pioner innen metallisk 3D-printing. Målet er nå å bygge videre på denne kompetansen og bringe den også i andre sektorer. Den vellykkede konklusjonen av NextGenAM representerer dermed en annen viktig byggestein i vår strategi, uttaler Thomas Ehm, styreleder for Premium AEROTEC.
Helautomatisert produksjonHemmeligheten ligger i en genial og skalerbar additiv produksjonskjede, som er helautomatisert helt til det punktet hvor de printede delene blir mekanisk saget av byggeplattformen. Dette innebærer at det ikke kreves noe manuelt arbeid på et hvilket som helst stadium av prosessen, fra dataforberedelse og sentralpulverforsyning til selve AM-prosessen, inkludert varmebehandling, kvalitetssikring og separasjon av komponentene fra byggeplattformen. Systemets tekniske hjerte er EOS M 400-4 fire-lasersystemet for industriell 3D-print ved bruk av metallmaterialer. Et førerfritt transportsystem og roboter sikrer jevn bevegelse av delene gjennom hvert trinn i produksjonslinjen.
Hele produksjonsprosessen går av seg selv, uten operasjonelt personell, fra et sentralt, autonomt kontrollsenter. Grunnleggende for systemet, og måten alle maskinene brukes på, er nettverksbasert. Byggejobbdataene overføres til kontrollsenteret, som deretter prioriterer de forskjellige byggforespørsler og tildeler dem til et AM-system. Under byggeprosessen kan produksjonsstatusen også hentes på en mobil enhet, uavhengig av sted. Når full produksjonskjede er fullført, sendes kvalitetsrapporter sentralt til kontrollsenteret. Alle dataene som er nødvendige for produksjon av en digital "tvilling", kan nås her, slik at det blant annet er mulig å få fullstendig sporbarhet.
- Vi er veldig stolte av hva vi har oppnådd i samarbeid med våre partnere Premium AEROTEC og Daimler. NextGenAM-prosjektet har gitt en veldig konkret demonstrasjon av hvordan industriell 3D-utskrift kan brukes kostnadseffektiv i serieproduksjon som en del av en automatisert prosesskjede. I kombinasjon med mulighetene for digitalisering som brukt her, representerer pilotanlegget ikke mindre enn en milepæl på vei til digital produksjon, sier Adrian Keppler, administrerende direktør i EOS.
Kapasiteten kan forlengesmEn kontinuerlig 3D-datastreng med integrert kvalitetsstyring gjør dette produksjonssystemet et av de første eksemplene på fremtidens referanse, Industry 4.0. Produksjonsprosessen er fullstendig skalerbar: produksjonslinjene kan enkelt dupliseres for å forlenge anleggets kapasitet. Dette gir løfte om ytterligere betydelige besparelser i fremtiden etter hvert som tallene stiger. I dag er pilotanlegget allerede i stand til å automatisere produksjon av komponenter til serieproduksjonskvalitetsstandarder.
Deler til Daimler produseres allerede på den nye teknologilinjen på Premium AEROTEC: lastebilenheten bruker for eksempel allerede den første reservedelen produsert på Premium AEROTEC. Dette er en brakett for en lastebildieselmotor.
Reservedeler til lastebiler og busser3D-printsprosessen er spesielt nyttig i reservedelsektoren siden, i tilfelle et verktøyproblem, kan sjeldne nødvendige deler ofte gjengis mer kostnadseffektivt enn ved konvensjonelle sand- eller press-støpeprosesser. De første forespørsler om 3D-printede bussreservedeler i aluminium blir for tiden undersøkt på kompetansesenteret for 3D-printing på Daimler Buses. Analyseteamet i personbilområdet vurderer for tiden egnede potensielle applikasjoner.
Muligheter for små serier og prototyping- Additiv produksjon er også egnet for små-serieproduksjon av nye biler (begrensede utgaver). Systematisk utvikling av delene spesielt for 3D-printing betyr at produksjonskostnadene kan reduseres ytterligere og kvaliteten optimaliseres, ifølge Jasmin Eichler, leder av fremtidige teknologier hos Daimler AG." 3D-printing gir også spesiell betydning under forutgående utvikling av kjøretøyer. Det lave antallet som kreves kan ofte produseres mer kostnadseffektivt, og raskere, med additiv produksjon enn med konvensjonelle produksjonsprosesser. "
Og dette gjelder like mye for biler med forbrenningsmotor som for elektriske biler. 3D-printing er også ypperlig egnet, for eksempel for produksjon av integrerte baseplater som bærer kjølelinjer for batteriene i elektriske kjøretøy.
For mer informasjon se: www.eos.info/nextgenam