Kompakt og smart produksjon i Övik
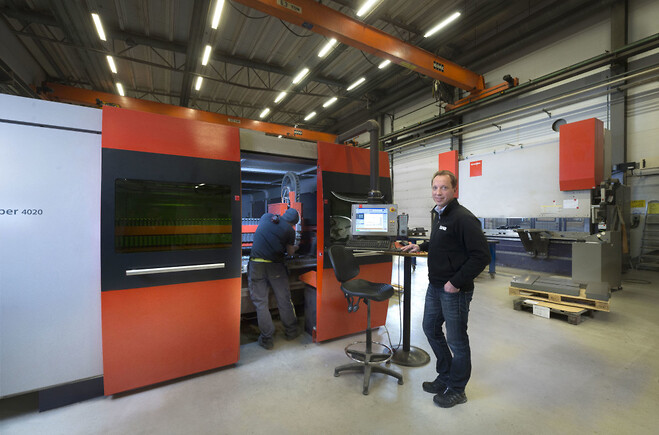
- Det er forskjellige størrelser, alt fra 1x1 cm opp til fire meter i lengde, der har vi har spennvidden på det vi produserer i laseren, vi har også vannskjæring der vi legger på ytterligere to meter, sier Andreas Byström administrerende direktør og medeier av verkstedet som ble bygget kun for produksjon av skjærte og/eller knekte deler. Selskapet Örnsköldsviks Skärcentra AB startet sin virksomhet i 2013. Det første som ble gjort var å investere i en 4 kW fiberlaser fra Bystronic.
- Vi var blant de første i Sverige med en fiberlaser og forventet å ha en omsetning på 15 millioner etter fem år. Nå med fasit i hånden ser vi at omsetningen er nær 35 millioner, og dette uten noen markedsføring overhodet.
Logistikken fungererBra jobbet, hvordan gjør man det?
- Det er business to business. Knuseanleggsprodusenten Jonsson & Söner er en stor kunde for å ta et eksempel, men vi har i prinsippet alle Örnsköldsviks produserende selskaper som kunder en eller annen gang i løpet av et år. Med så mange forskjellige artikler må du ha et fungerende system helt fra starten. Når vi skjærer ut hver eneste detalj graveres et artikkelnummer og ordrenummer på hver metallplate. Det er noen kunder som ikke vil ha det, så utelater man det så klart. Hver platedetalj får nå en identitet, og hvis en kunde ringer om et år og oppgir nummeret og sier at man vil ha 10 til av den bestemte biten, blir det en produksjonsordre så snart det siste sifferet er lagt inn. Det graverte tallet gjør at vi kan holde oversikt over tusenvis av produkter samtidig uten store problemer, sier Andreas.
Programmet som forenkler hele prosessenPlant Manager er et unikt program som er laget gjennom tusenvis av timer av Bystronics teknikere, som har som mål å maksimere laserskjæring på forskjellige nivåer. Hvis du trekker en parallell til å presse pepperkaker ut av en rullet deig, handler det om å få så mange pepperkakehjerter som mulig uten å måtte rulle ut deigen igjen. Når det gjelder laserskjæring av metallplater gjelder hundrevis av andre parametere. Avhengig av metallplatens tykkelse kan man ikke skjære for nær den andre delen, da varmeutviklingen fører til uønskede endringer i metallstrukturen. Dette gjelder bare for visse tykkelser, og også valget av plater spiller en rolle for at sluttresultatet skal være perfekt, men alt slikt er allerede i systemets enorme database og kan derfor maksimere skjæreplanene og hele prosessen.
- Plant Manager-programmet, sammen med selskapets materialer og planleggingssystem Monitor, holder oversikt over omstillingstider, tilbudsprosess og ledetider for andre operasjoner i verkstedet. De regner ut alle skjæreplanene under, la oss si en ti-dagers produksjon, og det minimerer tap og på den måten maksimerer overskuddet. Den største fordelen med maskiner fra samme leverandør, i dette tilfellet Bystronic, er at alle enhetene kommuniserer med hverandre. Programmet vet at detaljen skal bøyes x antall ganger senere i håndteringen og det tas hensyn tilk det, selv før laseren skjærer i platen. Resultatet blir en nøyaktig detalj hver gang, og man trenger ikke å lage en testbit, vi kan også simulere en kjøring med prosessen fra skjært detalj til ferdig knekking dersom omstendighetene krever det, sier Andreas.
Nyinvesteringen skapte plassAlle produserende enheter har flaskehalser. For ÖSAB var det den videre bearbeidingen i kantpressen som ble selskapets svake ledd. Fiberlaserskjæremaskinen og den nye måten å jobbe på med Plant Manager gikk så raskt at mange detaljer som skulle knekkes måtte vente.
- Tommelfingerregelen er at en lasermaskin mater to kantpresser, nå hadde vi en på 400 tonn fra før og så at en 200-tonner ville løse flaskehalsen i produksjonen. Det eneste problemet var at vi allerede var overfylt i verkstedet på 900 kvadratmeter. Skeptiske stemmer sa det for overfylt, men det viste seg at når vi kuttet ned ledetidene var det ikke behov for plass til detaljene som ventet på videre bearbeiding, men det ble isteden mer plass i verkstedet og raskere service for kundene, uttaler Andreas.
Tenker utenfor (den sveiste) boksenÖSAB er et velstående selskap fordi de er i forkant rent teknisk, men selskapets filosofi ligger også i at man liker å tenke i andre baner. Må man alltid sveise en fuge på en detalj som krever det? Nei, ikke alltid, mener Andreas:
- Maskinene er så presise i dag at du i noen detaljer kan lage et "klikksystem" der sidene på en struktur kan festes sammen med en kompresjon i stedet for å sveises sammen. Resultatet er det samme eller enda bedre, og kundene våre sparer penger. Det er et eksempel av mange på hvordan vi tenker hos oss. Av selskapets ansatte er fire fra andre land. Verkstedstrukturen for skjærende bearbeiding med etterbehandling er annerledes i dag sammenlignet med for 10 år siden. Maskinparken er så avansert at vi ikke kvier oss med å ansette folk uten tidligere erfaring, sier Andreas og peker på en fyr ute på verkstedet. Gå og spør ham hva han tidligere har jobbet med.
- Jeg heter Gabriele Greco og har eksamen i humaniora og har drevet et kunstgalleri i Firenze. Nå bor jeg i Övik og liker å organisere og strukturere alle detaljene som flyter gjennom verkstedet sier en smilende italiener. Så det ser ikke ut til å være en kunst å holde tusenvis av artikler i orden hvis du har den rette holdningen. Det har man i Övik!
For mer informasjon se: www.oesab.se og www.bystronic.com og www.itec.as